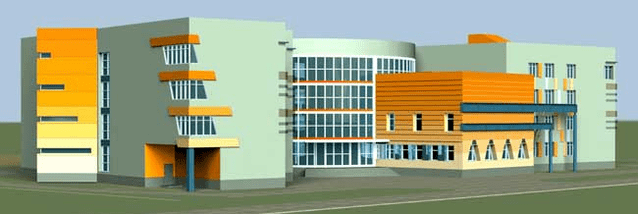
Energy saving in the enterprise - main directions:
- Saving electricity
- Reduction of heat and steam losses
- Reduction of losses in steam lines
Energy saving in the enterprise - Energy saving methods
- Selecting the optimal price category and reviewing the contractual terms of electricity supply
- Optimization of electric motors
- VFD installation
- Optimization of compressed air systems
Selection of the optimal price category for electricity supply
In total, there are 6 categories of electricity supply prices, according to which enterprises can buy electricity from guaranteed suppliers.
All small enterprises with an installed capacity of less than 670 kW, at the time of concluding a contract for an automatic power supply, fall into the first price category.
All enterprises with an installed capacity of more than 670 kW automatically enter the third price category.
The first and third price categories are not always the most optimal and cheapest categories of electricity supply.
In some cases, switching to another price category can reduce the cost of electricity by 5% -30%.
The topic of price categories is quite broad, in our review of price categories, we show in detail how to correctly calculate and select the price category of electricity supply.
In addition to price categories, we also recommend looking closely at other aspects of the power supply contract:
- voltage level,
- power,
- electricity transmission tariff.
In our review, you can learn about these and other methods to reduce energy costs.
Energy saving in the enterprise - Electric motors
It is necessary to consider all equipment where electric motors are used:
- pump,
- compressors,
- Fans,
- machinery tools,
- production lines.
Electric motor control plan
The motor control plan should become an integral part of the plant's energy conservation program.
Such a plan will help implement a long-term energy saving system for all electric motors in the enterprise.
The motor control plan will ensure that failures and malfunctions do not occur, and if they do occur, are resolved quickly and efficiently.
Steps to create a motor control plan:
- Make an inventory of all the engines in the facility.
- Create a list of engines with their main parameters, technical condition, service life.
- Develop general instructions for carrying out repairs.
- Develop maintenance, lubrication, and preventative inspection instructions.
- Create a backup of frequently used spare parts.
- Create a purchase specification for new engines.
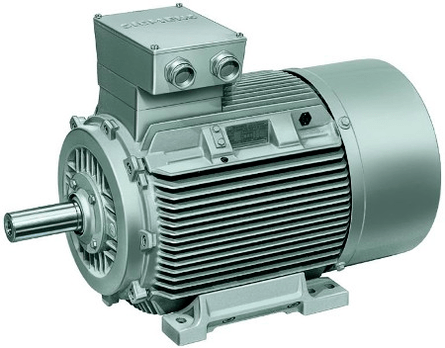
Rotation of electric motors
In general, returning an old electric motor is much cheaper than buying a new motor.
The electric motor must be replaced if the cost of returning it is more than 60% of the cost of a new one.
Then everything will depend on how the reversal is performed.
If the work is done at the highest level, then the engine will lose only 1% -2% percent of its efficiency.
If the return is performed poorly, then the losses in the electric motor will increase by 5% -10%.
Replacing the old electric motor with a new energy-efficient one makes sense in cases where the motor runs for more than 2000 hours a year.
The payback period for a new energy efficient engine will not be more than 1. 5 - 2 years.
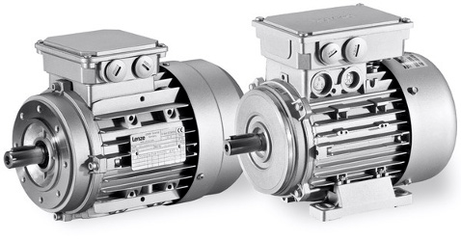
Saving energy in the enterprise by increasing the load factor
The load factor is the ratio of operating power to apparent power.
This is how efficiently energy is used.
The higher the load factor, the more efficiently electricity is used.
Electric motor operates optimally at 75% load and above.
Therefore, installing motors above the required power (for safety reasons) will not only be more expensive, but also inefficient in terms of power consumption.
The load factor can be increased as follows:
- shutdown of discharged engines,
- replacement of engines, which are less than 45% charged, for less powerful models,
- load redistribution between existing electric motors.
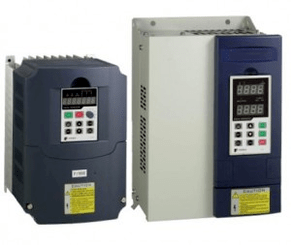
Variable Frequency Drive (VFD)
Installing variable frequency drives only makes sense for dynamic systems.
In static systems, which are included, for example, only for lifting loads, installing a variable frequency driver will not help and can often do harm.
VFD balances the load and speed of the motor, ensuring that electricity is used optimally.
VFD can reduce engine power consumption by a minimum of 5% and a maximum of 60%.
The payback period for VFD is usually 1-3 years.
Optimization of compressed air systems
Compressed air is used in a wide variety of industries.
In some enterprises, compressed air is the main consumer of electricity.
Compressed air is used in pneumatic equipment and devices, in conveyors, automatic lines.
The use of compressed air is popular because it is a convenient and safe source of energy.
But many people forget that compressed air is one of the most inefficient sources of energy - only 5% of the electricity spent on producing compressed air goes back to useful work, the remaining 95% goes to the pipe.
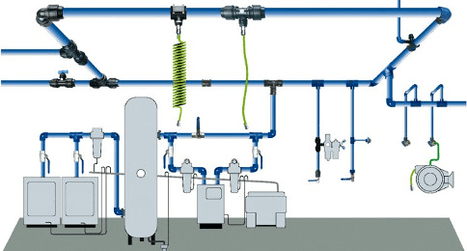
Energy saving in the enterprise - compressed air:
- Do not use compressed air to clean the premises.
- Reducing the air temperature at the compressor inlet by 3% reduces power consumption by 1%.
- For those technical processes, when possible, reduce the compressed air pressure to a minimum. Reducing the pressure by 10% reduces energy consumption by 5%.
- Perform regular inspections, repairs of compressor equipment and compressed air transmission lines. One, even the smallest flow of compressed air, can reduce the efficiency of equipment over time.
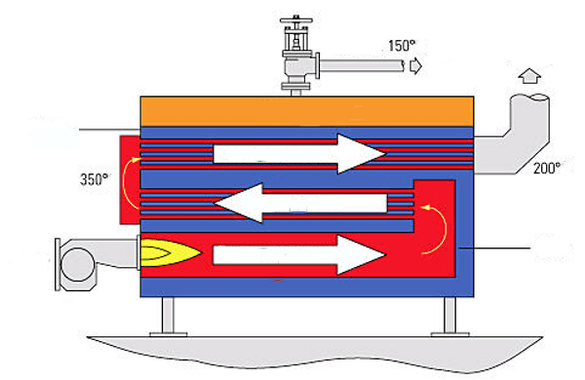
Energy saving in the enterprise - we reduce heat and steam losses
Steam is often used in industry, especially in the textile, food and processing industries.
Improving the efficiency of steam boilers and reusing the heat generated can significantly reduce energy consumption in these plants.
Steam production
The boiler works more efficiently at full power.
Due to the fact that the demand for the amount of steam can change over time, it often happens that the boiler operates under its optimal load.
The capacity of the installed boiler can be much higher than the needs of the enterprise, due to declining demand for products, or unfulfilled plans to expand production.
Also, boiler capacity may not be required due to improvements in the production process or the introduction of energy saving measures.
In such cases, the boiler works or not at full capacity, or in the mode of short shut-off cycles.
Both of these situations result in significant energy losses.
There are no simple and inexpensive solutions to this problem.
The easiest option isinstall a "small" boiler that will operate at full capacitywith a medium or low workload in the enterprise.
Despite the fact that this is not a cheap solution, the payback period for such an investment can be less than two years.
And, in general, it is always more efficient to have some small interchangeable boilers, especially in enterprises with changing demand or significant seasonal fluctuations in heat and steam consumption.
Automatic adjustment system
If the enterprise has several boilers, then it makes sense to installautomatic system for regulating the load of boilers. . .
Automation responds to the need for steam in the enterprise, by redistributing the load between the boilers, turning on or off the boilers, significantly increasing the efficiency of the whole system.
Gate valve
In enterprises where boilers are regularly shut down due to falling demand for steam, heat losses through the chimney can be quite high.
It is possible to block the loss of hot air through the chimneyby installing a gate valvewhich closes the tube when the boiler is off.
Prevention and maintenance
Left unattended, igniters and condensate return systems can deteriorate rapidly or fail.
This can reduce the boiler efficiency by 20% -30%.
A simple maintenance program - ensuring that all boiler components are operating at their maximum level - will significantly increase operating efficiency.
In practice, regular maintenance reduces boiler energy consumption by 10%.
Insulation - heat loss from the surface of a properly insulated boiler should be below 1%.
Removal of soot and scale
It is necessary to constantly monitor and eliminate the formation of soot in the boiler pipes, the degree inside the boiler.
A 0. 8 mm thick soot layer reduces heat transfer by 9. 5%, while a 4. 5 mm thick layer reduces heat transfer by 69%!
The scale is formed when calcium, magnesium and silicon are deposited in the boiler heat exchanger.
The 1 millimeter thick scale increases energy consumption by 2%.
Soot and scale can be removed mechanically or with acids.
The formation of soot and scale can be determined by an increase in the temperature of the flue gases or by visual inspection when the boiler is not in operation.
Soot and scale formation should be monitored especially carefully if the boiler works with solid fuels (coal, peat, firewood).
Gas boilers are less prone to soot problems.
Boiler shock optimization
Boiler discharge is the discharge of boiler water to clean the water inside the boiler from impurities and salts.
The purpose of hitting the boiler is to avoid or reduce scale formation.
Insufficient shock of the boiler can lead to water entering the steam, or the formation of deposits in the boiler.
Excessive shock means loss of heat, water and chemicals.
The optimal level of shock depends on the type of boiler, the operating pressure in the boiler, the preparation and the quality of the water used.
The first thing to pay attention to is the preparation of water. If the water is treated well (low salt content), the swelling rate can be 4%.
If there are foreign substances and salts in the water, then the swelling rate will be 8% -10%.
The automatic shock system can also significantly reduce power consumption.
The payback period for such a system is usually 1-3 years.
Reduction of smoke emissions
Excess smoke is often the result of air penetrating the boiler and chimney through leaks and openings.
This reduces heat transfer and increases the load on the compressor system.
Leaks and holes can be easily eliminated, it is only necessary to periodically perform a visual inspection of the boiler and chimney.
Air regulation
The more air used to burn fuel, the more heat is blown out.
An amount of air slightly above the ideal fuel / air stoichiometric ratio is required for safety reasons, to reduce NOx emissions and depends on the type of fuel.
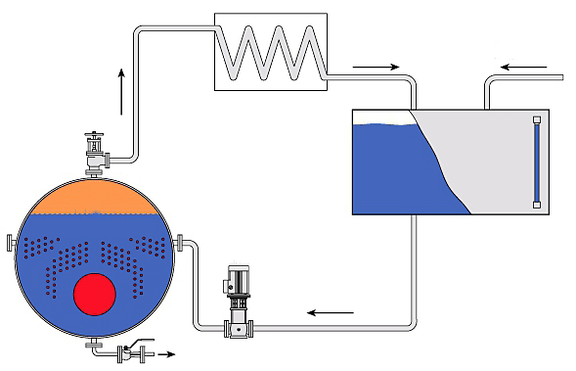
Boilers in poor technical condition can use up to 140% extra air, resulting in excessive smoke emissions.
An efficient gas burner requires 2% to 3% extra oxygen, or 10% to 15% extra air, to burn fuel without generating carbon monoxide.
The general rule is that the boiler efficiency increases by 1% for each 15% reduction of additional air.
Therefore, it is necessary to constantly check the fuel / air ratio.
This event costs nothing but has a very good effect.
Smoke emission monitoring
The amount of oxygen in the flue gas is the amount of extra air (added to increase safety and reduce emissions) and air that enters the boiler through holes and leaks.
The presence of leaks and holes can be easily detected if a monitoring system is installed for incoming air and the amount of oxygen in the flue gases.
Using data on the amount of carbon monoxide and oxygen, it is possible to optimize the fuel / air ratio in the boiler.
Installing a flu discharge monitoring and analysis system usually pays for itself in less than a year.
Energy saving in the enterprise - Installing an Economizer
The heat from the flue gases can be used to heat the water entering the boiler.
Hot water enters the boiler and requires less heat to be converted to steam, thus saving fuel.
The boiler efficiency increases by 1% for each drop of 22 ° C in the flue gas temperature.
The economizer can reduce fuel consumption by 5% - 10% and will be repaid in less than 2 years.
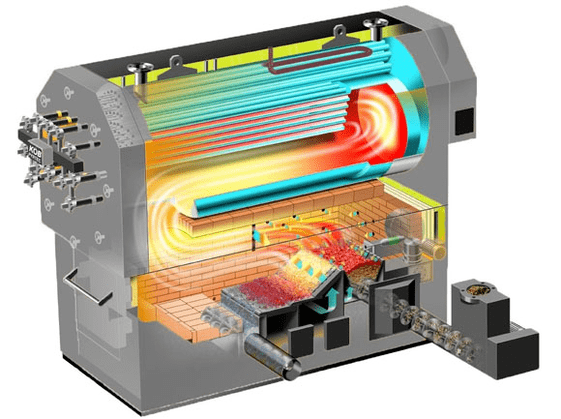
Heat exchanger to extract heat from water and steam from boiler blowing
The heat exchanger will help recycle about 80% of the water and steam heat from the boiler melting.
This heat can be used to heat buildings or to heat the water that feeds the boiler.
Any boiler with a constant blowing speed of 5% or more is an excellent candidate for a heat exchanger.
If the shock system does not work in a constant mode, then it makes sense to think about transferring it in a constant mode while simultaneously installing a heat exchanger.
The average payback period for a heat exchanger will not exceed 1. 5 - 2 years.
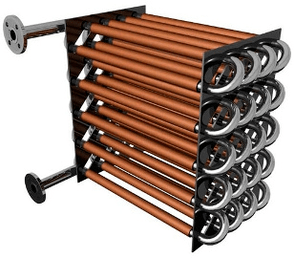
Installing a condensing economizer
Hot condensate can be returned to the boiler, thus saving energy and reducing the need for treated water.
Condensing economizer can increase system efficiency by an additional 10%.
The installation of such an economizer should be carried out under the close supervision of specialists who will take into account all the nuances of such a system, its effect on the boiler and the chemical composition of the water.
Using a system that returns condensate back to the boiler usually pays for itself in 1-1, 5 years.
A system that directs condensate into a hot water supply pays for itself in less than a year.
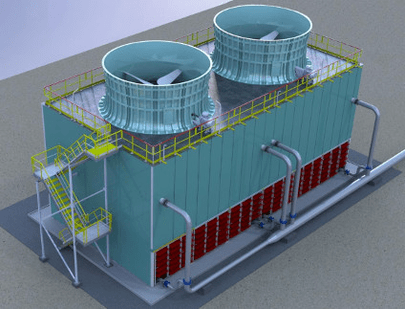
Cooling tower (cooling tower)
A cooling tower is a heat exchanger in which water is cooled by an air stream.
And in terms of energy efficiency, a cooling tower is a device that blows heat into the wind.
Energy saving potential in cooling towers:
- In some enterprises it makes sense to abandon cooling towers altogether. There are many cases where heating is used to heat a room and at the same time a cooling tower is used to distribute the heat. Installing a heat pump will solve the heat issue and at least partially reduce the need to use the cooling tower.
- Installing circuit breakers for cooling tower fans can reduce power consumption by 40%.
- Replacing aluminum or iron fans with new fans (with glass wool and plastic molds) can reduce energy consumption by up to 30%.
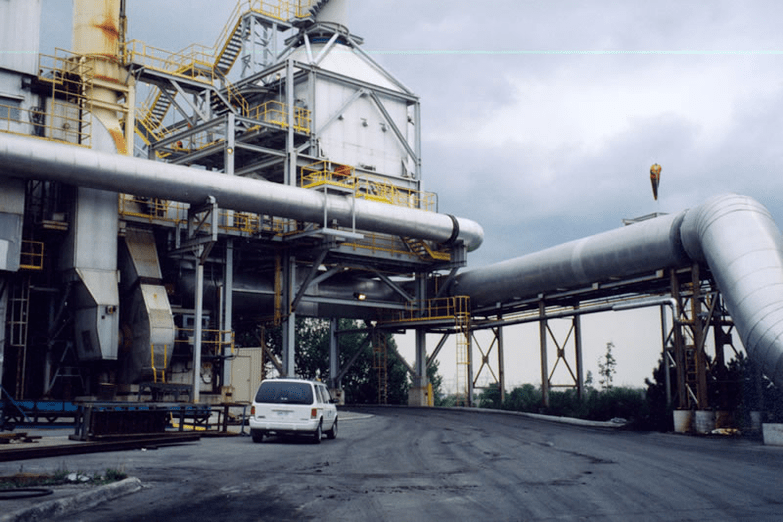
Reduction of losses in steam lines
Disconnection of unsolicited steam lines
Steam and consumption needs are constantly changing.
This can lead to the fact that the entire steam distribution system is not used at full capacity, but only 20% -50%, which inevitably leads to heat loss.
It is clear that optimizing or reconfiguring the entire steam distribution system to meet the new needs will be very costly and, perhaps, not feasible.
However, identifying and closing unused steam lines can be a very effective way to save energy.
Energy saving in the enterprise - Thermal insulation of pipes
Vapor insulating pipes can reduce energy losses by up to 90%.
This is one of the fastest returns on energy savings in the steam distribution system.
The average payback period for the insulation of pipelines through which steam or hot water is transmitted is about 1 year.
Condensate pipes for 1, 5-2 years.
Steam trap monitoring
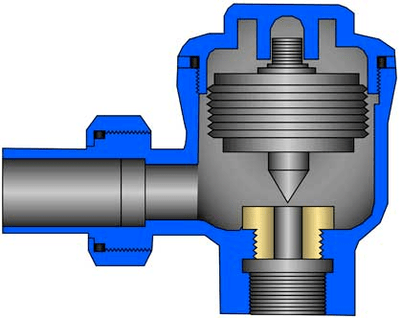
A simple monitoring program for the technical condition of steam traps can significantly reduce heat loss.
For example, if maintenance has not been performed for 3 to 5 years, then, as a rule, about one-third of the steam traps are out of order, allowing steam to penetrate the condensate drainage system.
From practice, in enterprises that have a monitoring program for steam traps, no more than 5% of steam traps are in the wrong condition.
The average payback period for replacing or maintaining a steam trap is less than six months.
A steam trap monitoring program will typically reduce steam losses by 10%.
Steam thermostatic traps
The use of modern thermostatic steam traps can reduce energy consumption and at the same time increase the reliability of the whole system.
The main advantage of thermostatic steam traps is that they
- opens when the temperature approaches the saturated vapor level (+/- 2 C °),
- emit non-condensable gases after each opening and
- are in the open state at the beginning of the operation of the system, which ensures its rapid heating.
Also, these steam traps are very reliable and can be used in a wide range of pressures.
Detachment of steam traps
You can reduce power consumption by turning off steam traps on overheated steam lines when not in use.
Elimination of steam leaks
A small hole steam leak repair program can pay for in less than 3 to 4 months.
We must not forget that small leaks can go unnoticed for years, constantly damaging the system.
Reuse of condensate and steam
When a steam trap discharges condensate from a steam system, the pressure drop creates steam from that condensate.
This steam, along with condensate, can be used in a heat exchanger to heat water or air.
Most importantly, it is possible to use this steam and condensate near the point of release, as it can be very costly to set up a separate piping system to transport it to the point of use.